Accounting for manufacturing businesses
Here’s what you need to know to navigate manufacturing accounting successfully, including the best practices for the industry, the most complicated processes involved, and some fundamental terms. By integrating your accounting software with Katana’s cloud manufacturing platform, you’ll get all these essential features and more. Get a demo of Katana, and see why thousands of manufacturers trust Katana to manage their entire business.
- If nothing else, it’ll help you analyze your financial statements and reports to improve the efficiency of your business.
- It helps businesses manage their finances, inventory, and cash flow and prepare for future production costs.
- The first-in-first-out (FIFO) inventory valuation method assumes that the first unit you manufacture is the first one you sell.
- Some of the benefits of having a Manufacturing account include increased efficiency, improved cash flow, better budgeting, greater flexibility, and the ability to save time and money.
- These insights enable businesses to optimize their inventory management strategies and achieve a more streamlined and profitable manufacturing process.
Cost accounting
It is therefore mostly an internal business management process aimed at better decision-making what is fcf how do you calculate it on budgeting, cost control, constraint and margin analysis, etc. The best accounting software for manufacturing businesses will also integrate with other software you use, such as your ERP software, CRM systems, or other modules that speak to inventory management and production. You should also be able to give access easily to any third-party professionals that may need access to your financial information, such as your tax accountant or bookkeeper.
This involves identifying potential concerns in the production process and finding appropriate solutions for them. Addressing the concerns will help you streamline production costs for better efficiency and allow you to run a lean manufacturing model that turns higher profits. If cash flow is a potential concern, addressing this constraint might involve securing manufacturing business funding beforehand to ensure it does not impede the overall production process in the facility. A final aspect of manufacturing that largely informs manufacturing accounting is production costing.
Cost of Goods Sold Manufacturing Account
Accounting for the industry’s expenses allows production managers to streamline and weed out any unnecessary steps in production present value of an annuity definition and also determine a competitive price for their products. Identifying the margin of profit you earn on the products your business creates and sells is an important part of manufacturing accounting. Margin analysis often involves tracking and accounting for all the costs involved in the production and then subtracting those costs from the total value those steps generate.
On your typical manufacturing balance sheet, you should have raw materials, work in process, and finished goods as part of your inventory calculation. You will also want a periodic or perpetual inventory system to track how many products you have in your production line at any one time. When investing in manufacturing accounting software, it’s important to find a system that contains all the features you need – and not too many that you’ll never use. If the software is too complex or too time-consuming to implement, you can end up without seeing any return on the investment.
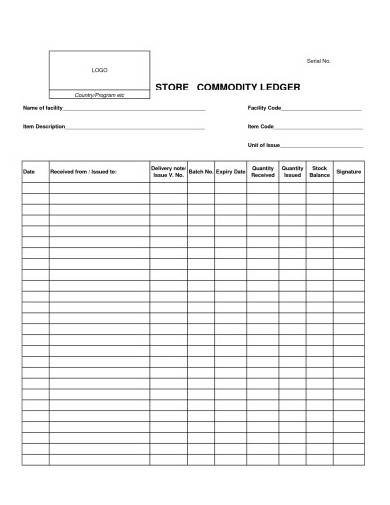
It integrates easily with third-party software solutions to help with project management. Invoiced is great for businesses that need to keep on top of their accounts receivable and invoicing. It automates everything from payments to reminders to collections, with the goal of getting your company paid faster — something most manufacturing companies need.
Table of Contents
These details enable the production managers to attune production practices to ensure the business remains efficient in production and saves costs while maximizing returns from sales. While keeping production costs to the minimum, businesses need to look to methods that allow them to make the best of their inventory, ensuring they produce quality products how to calculate inventory purchases while also sustaining seamless cash flow. From inventory and labor expenses to taxes and bookkeeping costs, accounting for manufacturing companies entails several aspects that need to be considered. A relevant exception is inventory valuation which generally needs to conform to local jurisdictions for taxing purposes.
Because manufacturers carry significant inventories, they need to know how to track their costs to create accurate financial statements and comply with accounting standards. It is crucial to select accounting software that seamlessly integrates with other essential programs, such as inventory management, production scheduling, and invoice generation. Compatibility with existing management tools and databases minimizes the risk of data loss or disruption to ongoing processes.
Very often, this is listed in a bill of materials, which itemizes quantities and costs the materials used in your product. In process manufacturing, such as food and beverage or chemicals, the bill of materials is known as a production recipe. To reduce the costs of doing business, you must understand first where your production costs lie. He's visited over 50 countries, lived aboard a circus ship, and once completed a Sudoku in under 3 minutes (allegedly).